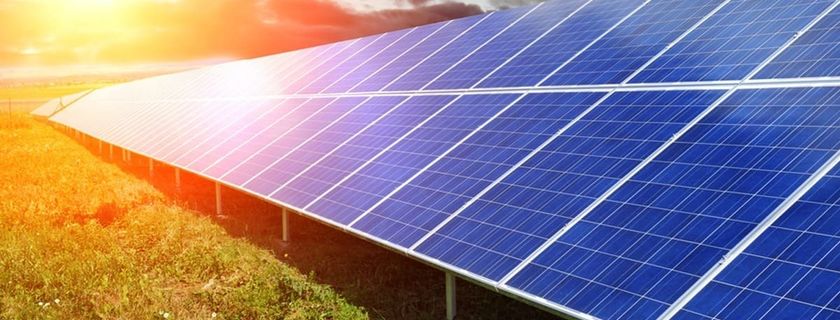
CIRCUSOL: Solar power business models towards a circular economy in Europe (PRESS RELEASE)
CIRCUSOL: Solar power business models towards a circular economy in…
Solar panel consists of multiple layers: silicon cells, polymer sheets, glasses, back sheet, and aluminium frames. The solar panel was designed very tightly to protect solar cells from degradation and without diminishing its possibility to harvest sunlight. The current design of solar panels does not allow to replace or repair solar cells as simply polymer and glass layers cannot be removed since they are integrated into each other. This is also a struggle with high-efficient recycling with the goal of recovery of all materials without losing their quality. Current methods involve manual removal of aluminium frames, junction box, and cables. The next steps involve mechanical shredding of panel or thermal heating to destroy the polymer's connections. Afterwards, the separation of materials uses methods such as magnet or sieving. Within our CIRCUSOL, SoliTek reviewed recycling technologies, alternatives to current materials used in solar panels, and methods of how to allow better management of the panels.
From the objective of reviewing current recycling technologies, SoliTek observed that there are advanced processes that do allow high-efficient recycling of silicon and thin-film panels. These processes usually involve chemicals that allow the purification of materials, such as the possibility to remove phosphorus from silicon. Chemical-based processes are also used for other multi-layer wastes, such as printed circuit boards (PCB) or food packages. One of the recent examples of high-efficient food packages recycling comes from DSM and APK companies developed a process that is already being used. It involves purifying polymers and removal of solvents in continuous circles whereas solvents are re-used again. As SoliTek has been seen co-operating with Lithuania universities working on recycling processes for solar panels and PCBs, recovery of chemicals used in the recycling process is crucial for reducing costs and maintaining low pollution. Currently, the main issues for the recycling of solar panels are:
Recovered materials through the mechanical process (aluminium, copper, and glass) can get about $3 in the U.S. according to Recycle PV Solar Company. With the high-efficient recycling process, the value can increase up to €5-€6 and more, if the materials can be up-cycled, such as converting materials like silicon to nano-particles.
In the next objective, SoliTek reviewed alternative materials to allow the solar panel to be easier to recycle and ended up with a fluorine-free back sheet, lead-free ribbon, and radio-frequency identification (RFID) technology. One of the concepts of cradle2cradle and circularity is to replace toxic materials. Fluorine-free back sheet and lead-free ribbons allow to achieve it. For lead-free ribbons, SoliTek has chosen bismuth as a replacement for the lead as it was commercially available by ribbon supplier and is less toxic than lead. Through the experiments, SoliTek has observed that bismuth requires lower temperatures in the soldering process (around 220 °C compared to 260 used for lead ribbons). Compared with lead-ribbons, there was about 30% lower strength of adhesion which should be enough for a solar panel. As SoliTek understood later, different types of process chemicals used in the soldering machine could lead to different soldering temperatures for bismuth. Bismuth has other issues as it is hard to recycle and has a high CO2 footprint due to being extracted together with other raw materials such as lead as alone extraction would be too costly. The RFID technology relies on replacing barcodes with chips which can store digital information in-themselves to allow solar panels to be digitalized. In past months, solar panels manufacturer AE Solar began to integrate RFID family-based NFC chips into the panels allowing it to be scanned by phone. This permits to access solar panel through mobile and have it connected to the database to retrieve relevant information or insert additional data. The enhanced barcode can allow better information handling about materials content, technical data, and history of the panel which can ease the transition to the second-hand market or recycling phases. The first two design options of lead-free ribbons (probably not bismuth due to its flaws) and fluorine-free back sheet combined with an enhanced barcode can increase the circularity of the panel.
All these design changes require to be tested to see if they truly bring benefits to the supply chain. It is also important to test whether panel performance does not decrease from the new materials used as then there would be a trade-off between generating more green electricity. Together with IMEC, SoliTek is testing two batches of 6 mini-modules each having bismuth-based ribbons, fluorine-free back sheet, and various RFID and NFC tags. Currently, there is no sign of degradation in the back sheet. Some RFID tags show clear deformations and some of them cannot be scanned after the climate chamber tests.
One of the objectives within CIRCUSOL was to look for design of the panel which would allow easier disassembly process. The next steps are to work with LuxChemtech to look for solar panel design which would be easier to recycle based on their innovative recycling processes. Another step is to finalize with testing RFID functions that CIRCUSOL partners Futech and IMEC had begun. The final step is to see if those mini-modules with alternative materials decrease the costs of recycling. Inputs will be used for CIRCUSOL partners to create viable business models.
CIRCUSOL: Solar power business models towards a circular economy in…